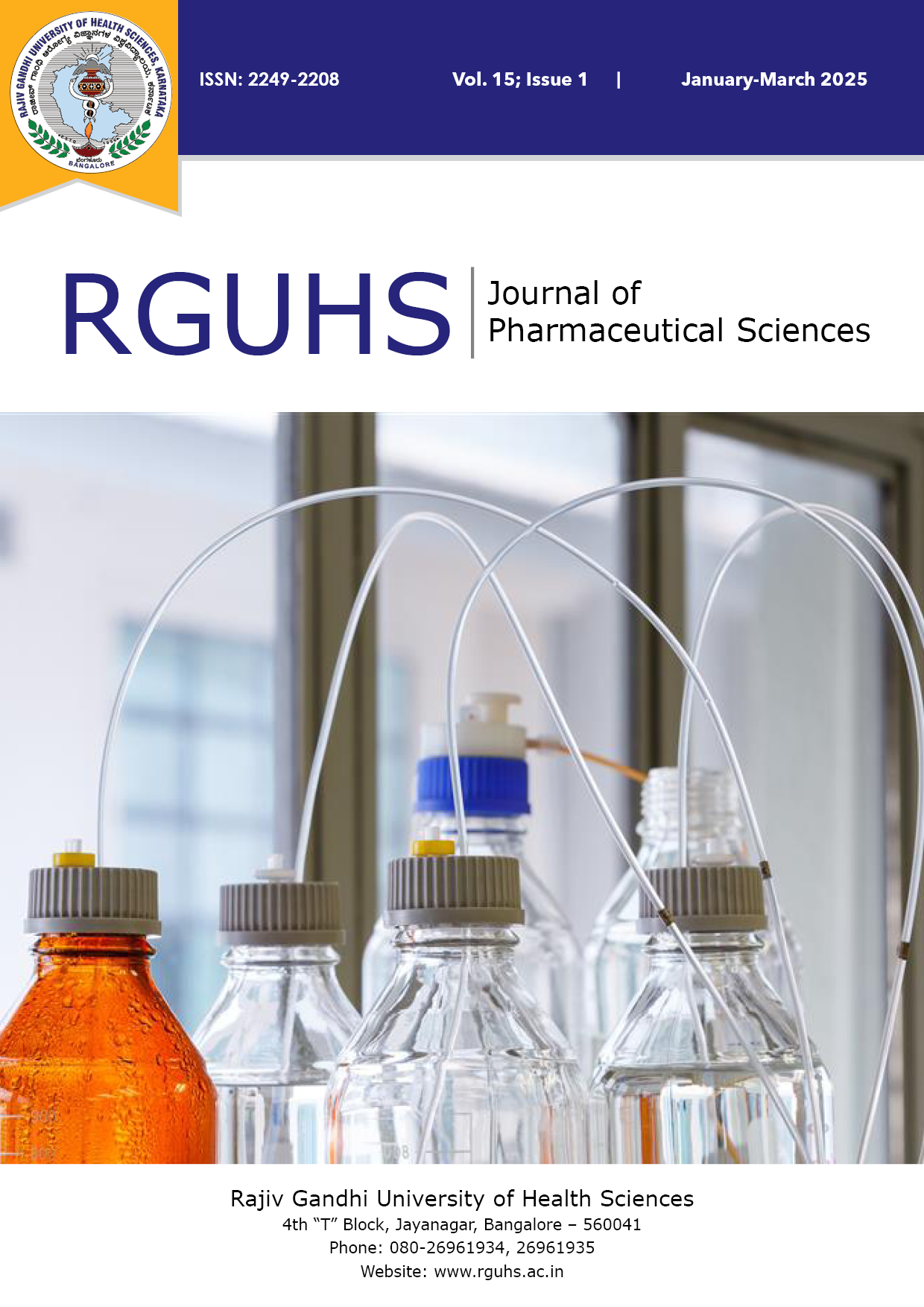
Abbreviation: RJPS Vol No: 15 Issue No: 1 eISSN: pISSN:2249-2208
Dear Authors,
We invite you to watch this comprehensive video guide on the process of submitting your article online. This video will provide you with step-by-step instructions to ensure a smooth and successful submission.
Thank you for your attention and cooperation.
1Vasanth Kumar PM, SVU College of Pharmaceutical Sciences, SV University, Tirupati, AP, India
2SVU College of Pharmaceutical Sciences, SV University, Tirupati, AP, India
3SVU College of Pharmaceutical Sciences, SV University, Tirupati, AP, India
4SVU College of Pharmaceutical Sciences, SV University, Tirupati, AP, India
5SVU College of Pharmaceutical Sciences, SV University, Tirupati, AP, India
*Corresponding Author:
Vasanth Kumar PM, SVU College of Pharmaceutical Sciences, SV University, Tirupati, AP, India, Email:
Abstract
Background: Rabeprazole sodium is a proton pump inhibitor, used for the treatment of peptic ulcer and gastroesophageal reflux disease by inhibiting the enzyme H+\K+ATPase, the acidic pump. In addition, erosive esophagitis and Zollinger-Ellison syndrome are treated with it.In this study, the objective was to develop a pharmaceutically stable and cost-effective and quality-improved formulation and UV spectrophotometry method have been developed to estimate Rabeprazole sodium delayed-release tablets. To achieve these goals, various prototype formulation trails will be taken and evaluated.
Methods: Rabeprazole sodium prolonged release tablets were prepared by direct compression technique used to the different excipients, as well as varying concentrations of polymer proportion using HPMC phthalate 55 which is an enteric coating material.
Results: The results indicated that the final product formulation 12 met all the specifications of the physical properties and invitation release and is comparable to the innovator product.
Conclusions: In the present study, Rabeprazole enteric-coated tablets were prepared using HPMC phthalate 55, enteric polymer. Formulation 12 was found to be the best of all formulations showing drug release that matches the innovator product, so all quality control tests were performed for conformation for the formulation. The tablets were tested for acid release during the stability period and the results confirmed that the results were within the limits.
Keywords
Downloads
-
1FullTextPDF
Article
Introduction
An extended-release dosage form aims to release the medication at a later time than immediately after ingestion. When the dosage form reaches the desired place or over a certain period of time, dosage forms can be made to change the drug release.1,2
When they reach the small intestine, enteric coatings that remain intact in the stomach breakdown and release the contents. Their main goal is to postpone the release of medications that can cause nausea or bleeding by irritating the gastrointestinal mucosa, being inactivated by stomach contents, or both.3,4,5,6
The class 1 BCI drug rabeprazole is distinguished by its high solubility and high permeability. The dependent factor, the dissolving rate, was selected to trace any effects of modifications to the formulation parameters. The final common stage in stomach acid secretion is inhibited by the group of drugs known as proton pump inhibitors substituted benzimidazoles, of which rabeprazole is a member. Inhibition of the enzyme H+/K+- adenosine triphosphate, which is found in gastric parietal cells, is the main mechanism of action. Regardless of stimulation, the effect on the last stage of gastric acid production reduces gastric acid production both under basal conditions and during stimulated acid secretion.
Materials and Methods
Materials: Rabeprazole sodium, mannitol, Crospovidone, sodium carbonate, ethyl cellulose, HPMC Phthale55, dehydrated alcohol, diacetylated monoglycerides, HPC, pigment yellow blend.
Method: Rabeprazole sodium, prolonged-release tablets was prepared using a direct compression technique using a different excipient as well as varying the concentrations of polymer proportions, using HPMC phthalate 55 as an enteric coating material. Detailed composition of rabeprazole sodium enteric-coated tablet formulations is given in the table below (Table 1).
Evaluation Parameters
Hardness:7
To withstand the stress of handling during its production, packaging, shipping, and dispensing, tablets need to have a specific level of mechanical strength. For drugs with prolonged release or other medications that have real or potential bioavailability problems or that are sensitive to changes in the drug release profile, it may be especially crucial to keep tabs on the tablet hardness. Using a Monsanto hardness taster, the crushing force needed to simply break the tablet is measured. The tablet is vertically placed between the bottom and upper plungers. A point moved along a gauge in the barrel to show pressure as the spring was squeezed.
Thickness:8
Once, tablet size and shape have been established, tablet thickness remains the only overall dimensional variable. The thickness should be within 5% or less than the established standard value. Tablet thickness variations that are too great can affect both packaging and consumer acceptance. A variation in the tablet thickness can indicate force. The thickness of the individual tablet was measured with a Vernier caliper.
Weight variation:9
The weight of each pill was recorded, the mean weight of the tablets was calculated, and the percentage variation of each tablet from the mean was determined.
Friability:10
The weight of 10 tablets was recorded, and then we put them in a Roche-type Friabilator, which uses a plastic chamber that rotates at 25 rpm while rolling the tablets a distance of 6 inches with each revolution. The preweighed tablet sample is then removed after 100 revolutions, dusted, and reweighed. Tablets that lose less than 0.5 to 1% of their weight are typically considered acceptable.
Disintegration test:11,12
Six tablets using a disintegration test apparatus with discs in a 0.1N HCL (Ph 1.2) maintained at 37 ± 2℃ for 2 hours. After 2 hrs, 0.1 N HCL is replaced with 6.8 PH buffer. A disc was added to each tube and operated for another 60 min. The rate of disintegration of each tablet was observed.
Analytical technique:
Rabeprazole sodium estimation: A 10g/ml of medication rabeprazole sodium solution was made by dissolving it in distilled water. In a UV-VIS spectrophotometer (double beam), Shimadzu, Japan, between a further dilution of the same and a scan for maximum absorbance (max) using distilled water as a blank, the UV ranges from 200 to 400 nm.
Rabeprazole calibration curve: In order to make sodium, 10 ml of distilled water was used to dissolve 100 mg of rabeprazole sodium. The volume was then increased to 100 ml using the same solution.
The previous stock solution of the drug was then diluted with distilled water to obtain 2, 4, 6, 8 and 10µg of the drug per ml. Then, using a double beam UV spectrophotometer and a blank of distilled water, the absorbance of the diluted solutions was determined at a maximum of 272.2 nm.
Accuracy and precision studies:
The enteric coated Rabeprazole tablet was used to extract the entire amount of medication contained in the tablet, sodium was crushed to a powder in a mortar and pestle. 100 milligrams of this powder were then added to the volumetric flask is containing a pH 9.0 buffer, then left aside for 24 hours with constant shaking. After an appropriate dilution, the absorbance of the solution is measured at a 272.2 nm using blank pH 9.0 buffers without any drugs. They copies of each reading were averaged. Using the established analytical approach, the drug recovery content was determined.
Results
This study was carried out to produce enteric-coated tablets with rabeprazole. The study includes drug preformulation and excipient studies, formulation and treatment development; the results of the above studies are presented in Tables 2 and 3.
The tablets were white to slightly yellowish-white solid very soluble in water and methanol with a bulk density of 0.5214 gm/ml. The melting point cannot be determined because a gradual degradation of rabeprazole during heating was observed. The weight of 12 formulations varies from 1.18-1.65, hardness from 8.4-9.6, thickness from 4.04-4.10, friability from 0.18-5.57, and disintegration time from 1.44-3.18 minutes.
Dissolution studies: The dissolution was carried out for different experimental trials and also for the innovator. The various results that are obtained are mentioned in Table 4.
Stability study
For all pharmaceutical dosage forms, it is important to determine the stability of the dosage form. This involves both normal and elevated temperatures, along with appropriate extrapolations to a guarantee that the product will, over the duration of its intended shelf life, provide medication for absorption at the same rate as when it was first developed. The behavior, characteristics, and formal stability studies of drug substance should be taken into consideration when designing formal stability studies of drug product. The issue of multiple acceptable criteria for release and shelf-life parameters, as well as a list of tests referencing the analytical technique and the proposed acceptance criteria, is addressed in ICH standards.13,14,15 Tables 5 and 6 present the stability, accuracy and precision studies results of rabeprazole sodium.
Discussion
The aim of the study was to formulate and evaluate prolonged release tablets of rabeprazole sodium, compared to innovative products. Twelve delayedrelease tablet formulations were prepared by direct compression. The analytical technique designed to estimate the sodium of rabeprazole in bulk fluids revealed a maximum absorbance of 272.2 nm and 400 nm. According to the analytical measurements mentioned above, the established UV spectrophotometry method for rabeprazole sodium was simple, accurate, precise, and repeatable. The results showed that the finished that the finished products formulation F12 meets all the physical property and in vitro release specifications and is comparable to be a starting product. Formulations 1 through 11 failed, for various reasons, such as lower acid resistance than the inventor’s formulation, higher impurity profiles during shelf life, or lower in vitro drug release than the inventor’s formulation. Although all preparations release the active ingredient, they are not comparable to the breakthrough product with rabeprazole sodium in the form of tablets of prolonged release. Twelve different formulations of enteric coated tablets were made using a direct compression approach. The results showed that the final formulation of the F12 product met the criteria of an innovative product in terms of both in vitro release and physical properties. Formulation F1 through F11 failed for a variety of reasons, including lower acid stability than innovator, higher impurity profiles during stability, and lower in vitro drug release than innovator. Although all pharmaceutical formulations are currently available on the market, they are not comparable to innovative products.
Conclusion
Rabeprazole sodium is a proton pump inhibitor that is used for the treatment of stomach ulcers. In this study rabeprazole coated tablets were manufactured by using HPMC 55 phthalate, which is an enteric polymer. Twelve enteric-coated tablet formulations of rabeprazole were prepared. F12 proved to be the best of all formulations showing drug release consistent with the new product. Therefore, all conformational quality control testing was performed on this formulation. The stability study is conducted at 25°C for 3 months; 60% relative humidity and 40; 75% relative humidity according to the ICH guidelines. According to ICH recommendation, the stability test is carried out at 25°C, 60% RH and then 40.75% RH for 3 months. During the stability period, the tablets were tested for acid release during the stability period, and the results were confirmed to be within tolerance and within limits. The formula is used for formulation and then other research to successfully bring the product to market. The maximum ultraviolet absorption of carbeprazole sodium in distilled water was measured at 272.2 nm, which is quite close to the published value of 284 nm. Then, according to the investigations of physicochemical characterization, the resulting bulk sample was pure, and the analytical work for rabeprazole sodium estimate was found to meet with beer’s limit in the range of 2.00g/ml to 10.00g/ml with the curve being linear.
Conflict of Interest
Nil
Supporting File
References
- Williams A. Pharmaceutical Manufacturing Encyclopedia. 3rd ed. Volume 1.
- Lee TWY, Robinson JR. Remington: The Science and Practice of Pharmacy. 20th ed. 2000. Lippincott Williams and Wilkins, Maryland. p. 1069-70.
- Wise DL. Handbook of Pharmaceutical Controlled Release Technology. 2000;473.
- Loyd V., Allen J, Nicholas G. Popovich, Howrad C. Ansel: Pharmaceutical Dosage Forms and Drug Delivery System. 8th ed. 2006. Lippincott Williams and Wilkins, Philadelphia. p. 260-275.
- Saptarishi D, Mukul S. Modified release dosage form and drug delivery. J Pharm Res 2009; 2(11):1728-29.
- Olsen K, Ghebre-sellasie I. Pharmaceutical Palletization Technology. 1st ed. 1989. Marcel and Dekker, New York. p. 39-69.
- Felton LA. Encyclopedia of Pharmaceutical Technology. 3rd ed. 2002. Marcel and Dekker, New York. p. 1-21.
- Patel PM, Desai HJ, Patel RC, Patel NM. Spectrophotometric method for estimation of rabeprazole. Indian J Pharm Sci. 2007;69(2): 318-320.
- Cassia V. Gargi, et al. Development and validation of dissolution test for Rabeprazole sodium in coated tablets. Int J Pharmaceutics 2007;120-125.
- Mukesh P. Ratnaparkhi, Mohanta GP, Lokesh Upadhay. Review on: Fast dissolving tablets. J Pharm Res 2009;2(1):5-12.
- Sharma A, Shukla T, Indoria M, Jha S. Design, Development, and Evaluation of Aceclofenac Sustained Release Matrix Tablets. Int J Drug Dev Res 2011;6(2):18-22.
- Sandeep Divate, Kunchu Kavitha, Ganesh Nanjan Sockan. Fast disintegrating tablets and emerging trends. Int J Pharm Sci Rev Res 2011;6(2):18-22.
- Ramakrishnan PN, Palanichamy S. Pharmaceutics-1. 11th ed. Jai Publishers, Madurai. 2007;147.
- British Pharmacopoeia. British Pharmacopeial Commission, London. 2000;2:209,299.
- The United States Pharmacopeial 24/NF 26. Asian ed. The official compendia of United States Pharmacopeial Convention Inc. Rockville. 1995:1015-1016